Indra, l'apprenti sorcier de la batterie recyclée
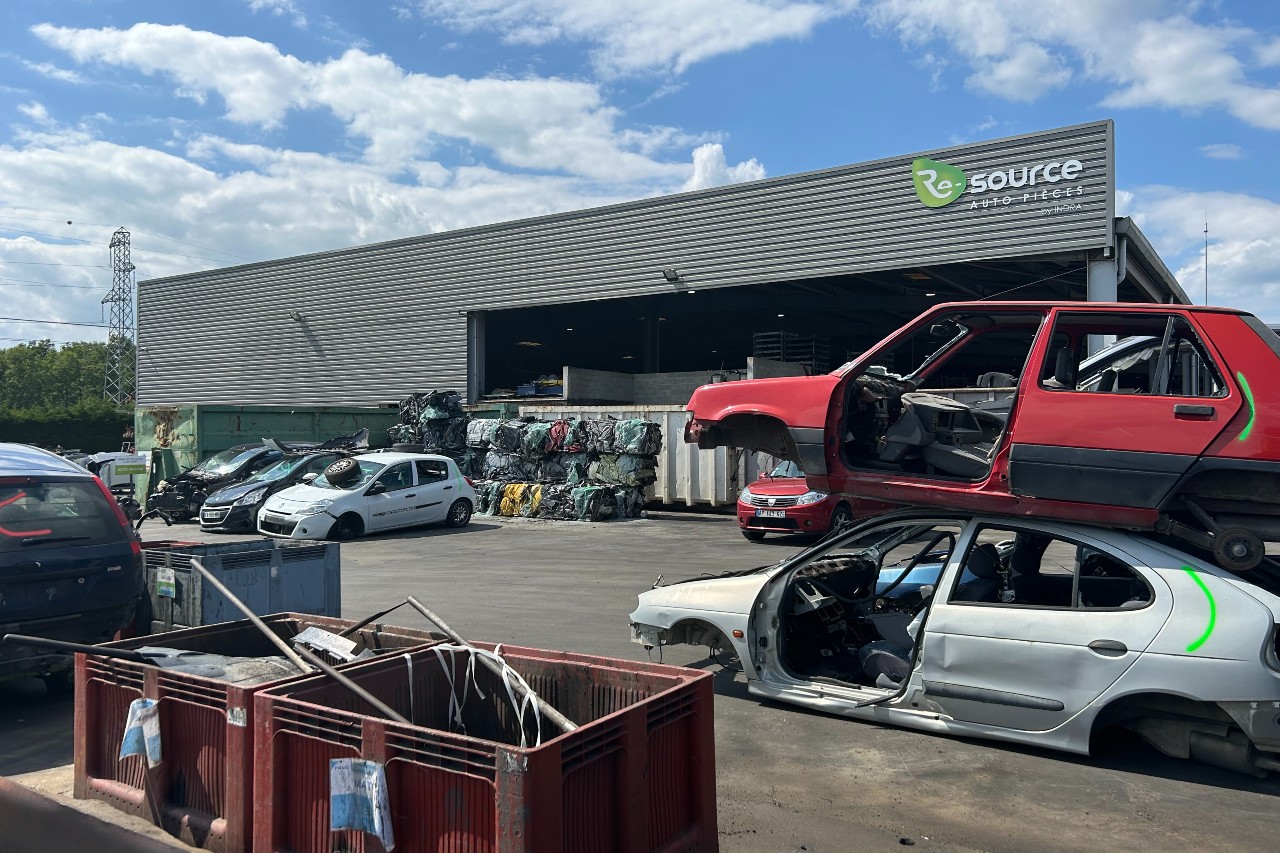
S’ils ne représentent qu’1 % des véhicules hors d’usage, toute la filière du recyclage se penche déjà sur la question des véhicules électrifiés. Deux semaines à peine après la présentation par Mobilians d’un guide pratique à destination des recycleurs pour le traitement de ces véhicules, Indra profite de la 11e édition de son Forum filière VHU pour présenter son savoir-faire en la matière.
Dans la zone commerciale de Prunier-en-Sologne (41), proche de Romorantin et de Vierzon, Indra possède l’un de ses trois centres VHU. Baptisé ReSource, l’établissement est particulièrement connu pour sa ligne industrialisée de démontage qui permet de désosser 4 000 véhicules par an. En comptant l’ensemble de ses trois centres, situés aussi à Sète et Auxerre, Indra recycle près de 10 000 véhicules par an. Sur les 1,3 million de VHU traités à l’échelle nationale, le réseau de 327 centres VHU d’Indra en démonte près 375 000, ce qui représente 28 % du marché, selon sa directrice générale Florence Bailleul.
Le traitement des véhicules électrifié façon Indra
L'intérêt d’Indra pour les véhicules électriques ne date pas d’hier. En effet, la coentreprise de Renault et Suez a réalisé un process spécifique pour le traitement des voitures électriques dans son centre ReSource qu’elle développe depuis plus de dix ans. Pour la présentation du dispositif lors du Forum filière VHU, Indra a fait l’étalage des divers équipements nécessaires au démontage d’un véhicule électrifié. Indra se présente comme un laboratoire pour son réseau, mais aussi pour toute la filière.
A lire aussi : Mobilians fixe les bonnes pratiques des recycleurs de batteries
Si le chemin vers le démontage d’un véhicule thermique est maitrisé, les VE nécessitent une attention particulière du fait de la batterie. Le démontage de cette dernière ajoute sept nouvelles étapes par rapport au même processus d’un véhicule classique. "Indra a déposé et mis en sécurité une centaine de modèles électrifiés à travers nos activités, et nous menons des prestations de dépose et de mise en sécurité pour les constructeurs et les concessionnaires", explique Allan Anchisi, directeur des opérations et du marketing.
Les centres VHU ont tout intérêt à récupérer la batterie pour le recyclage qui représente plus de 50 % de la valeur d’un VE. Cobalt, nickel, lithium, cuivre ou encore graphite, les métaux rares sont de plus en plus prisés et coûteux. Leur récupération devient donc un enjeu stratégique pour les constructeurs. Le recyclage de la batterie pourrait devenir la pièce manquante pour limiter les coûts, que ce soit en termes de seconde vie ou de récupération de matière.
La batterie, un élément à prendre avec des pincettes
Mais pour un centre VHU, la batterie ne doit pas être prise à la légère. Le risque numéro un : l’emballement de la température pouvant causer des incendies. Un risque qui peut être provoqué plusieurs heures, voire plusieurs jours après un choc. Les recycleurs doivent donc manipuler les voitures électrifiées avec la plus grande précaution, en particulier en ce qui concerne le stockage et le transport des batteries. Catégorisée 9 dans le code ONU elles sont considérées comme "matières et objets dangereux divers". Les dépanneurs transportant un véhicule électrique doivent respecter la norme ADR (règlement international pour les transports) et TMD (norme française complémentaire).
A lire aussi : Qu'est-ce que le "full life cycle management" que les constructeurs automobiles veulent instaurer ?
Il en est de même pour le stockage. Les risques d’incendies provoqués par les batteries au lithium sont loin d’être un mythe. En février 2024, un incendie s’est déclaré dans un bâtiment du groupe Snam (Société nouvelle d’affinage des métaux), à Viviez dans l’Aveyron. Ce bâtiment stockait notamment 900T de batterie au lithium. Ainsi, pour éviter ce genre d’incident, plusieurs solutions sont possibles, telles que des cellules d’immersion pour véhicule électrique ou encore les caissons d’intervention pour les batteries au lithium ayant subi un choc ou un incendie.
Comment réceptionner un VHU ?
La stratégie de ReSource pour réceptionner la batterie repose essentiellement sur son analyse. Afin de mesurer les risques, le VHU électrique fait l'objet d’un premier état des lieux visuel pour déterminer la méthode et la localisation du stockage (Doit-il être protégé des intempéries ou complètement mis en quarantaine ?) et d’un second plus approfondi. Cette étape doit permettre de vérifier l’état des différents composants. À l’issue, la batterie peut donc être considérée "sans dommage", "avec dommage" ou "réactive".
En fonction des process des constructeurs, la batterie peut être amenée à être mise hors tension. Une opération qui consiste à déconnecter les circuits. Mais actuellement, aucun constructeur ou fabricant de batterie n’a donné de consigne claire pour la collecte de la batterie. Une situation qui interroge de nombreux recycleurs. Après avoir réalisé un diagnostic complet du véhicule et une évaluation des risques, les équipe d’Indra s’affairent à la dépose de la batterie. Un pont mobile a été élaboré spécialement pour permettre de travailler la dépose du véhicule électrique dans une zone aérée et sécurisée. Le dispositif nécessite deux techniciens. Une mise en sécurité réalisée avec une table élévatrice a été spécialement développée pour la découpe de batterie.
Le stockage en sécurité
"Quand le véhicule est vraiment endommagé, la batterie peut se retrouver déformé, et cet outil est vraiment unique, puisqu’il nous permet aussi de traiter ces modèles très accidentés", souligne Allan Anchisi. La batterie est ensuite conditionnée dans différents types de caisse spécifique en fonction de la dangerosité de la batterie.
"Plus on rentre dans des caisses isolantes et sécurisées, plus leur coût est élevé", renchérit Allan Anchisi. Ces contenants disposent de système de détection en cas d’emballement thermique ou de détection de fumée. En cas d’anomalie, un système d’extinction s’active et les batteries sont noyées pour éviter tout risque d’incendie. Celles qui sont diagnostiquées en bon état peuvent être stockées dans des containers moins sécurisés. Finalement, tout découle du diagnostic initial.
Il existe plusieurs emballages spécifiques pour sécuriser une batterie dans le cadre de son transport. Celles qui sont diagnostiquées "réactive" se retrouvent dans un emballage "P911". La batterie dite "rétrogradée", qui représente de facto un risque moindre, peut se retrouver dans un emballage P908, moins coûteux que le précédent.
Réutilisable, le prix de ces dispositifs oscille entre 20 000 et 40 000 euros pour les P911 et 1 000 et 3 000 euros pour les emballages P908. Il y a deux semaines, le vice-président du métier Recycleurs de Mobilians, Laurent Hérail estimait entre 20 000 et 200 000 euros les investissements des centres VHU pour accueillir les véhicules électrifiés.
ReSource, le cobaye de la profession en matière de VE
Dans le cadre de la responsabilité élargie des producteurs (REP) ce sont les constructeurs qui doivent proposer un process de conditionnement aux centres VHU. Ces derniers doivent tester des conditionnements avec les différentes batteries. ReSource s’appuie donc sur leurs directives et s’adapte pour appliquer les bonnes pratiques de mise en sécurité de l’accu.
"Dans un monde idéal, il faudrait que ce soit le centre VHU qui soit responsable de la dépose et de la mise en sécurité de la batterie et que les constructeurs soient en responsabilité du transport de ces dernières et de son traitement. Nous passons notre temps à les challenger, car nous voyons ce qui ne va pas pour qu’ils déterminent les solutions à mettre en place dans la filière recyclage", assure Mouhammad Coulibaly, responsable prestation méthode d’Indra.
A lire aussi : Recyclage des batteries : la filière se construit
Aujourd’hui, le business model d’un centre VHU repose sur les véhicules thermiques et sur la pièce. Demain, avec les véhicules électriques, les pièces seront sur la carrosserie et la batterie. Pour qu’un centre VHU trouve un équilibre financier, il faut qu’il trouve son intérêt à générer du revenu au travers de la batterie.
"L’aspect recyclage a un coût pour un centre VHU. La filière tente de se structurer et cherche à générer du business au travers de la vente soit de la batterie pour de la seconde main. Mais cela pourrait aussi se caractériser par la vente de modules sains pour les injecter en réparation de batterie ou pour d’autres marchés", imagine Allan Anchisi.
Un processus compatible pour tous les modèles
L’activité de démontage des véhicules électriques est compatible avec la majorité des modèles. L’activité ReSource d’Indra a documenté un grand nombre de modèles et s’est forgé une base de connaissance qu’elle commence à mettre à disposition d’un certain nombre de centres VHU.
Au sein de son réseau, Indra tente de créer des centres "Expert VE" en leur partageant le savoir-faire acquis avec ReSource. Cela se traduit par de la formation d’opérateurs, du partage d’équipements et de la mise en place de process en fonction des modèles.
"Pour une Zoé, c’est un cas d’école, et le traitement prend deux heures maximums. Dans d’autres cas, l’accessibilité va être beaucoup plus longue, et il faut passer par de la dépollution dans un premier temps. Il faut compter quatre heures pour certains modèles, voir, une journée", affirme Mouhammad Coulibaly
A lire aussi : Stellantis s'allie à Orano pour le recyclage de batteries
Le traitement des batteries est en plein développement, et de nouvelles technologies apparaissent sur le marché. Certaines solutions sont mises en place pour le traitement des batteries. Des pistes sont aussi lancées sur la seconde vie des modules. Indra développe ainsi plusieurs équipes de R&D où les sujets sont sourcés et travaillent avec différents partenaires. L'intérêt est de bien structurer toute la filière.
Sur le même sujet
Laisser un commentaire
Vous devez vous connecter pour publier un commentaire.