Comment le groupe Renault rend ses usines plus efficientes grâce à l’IA
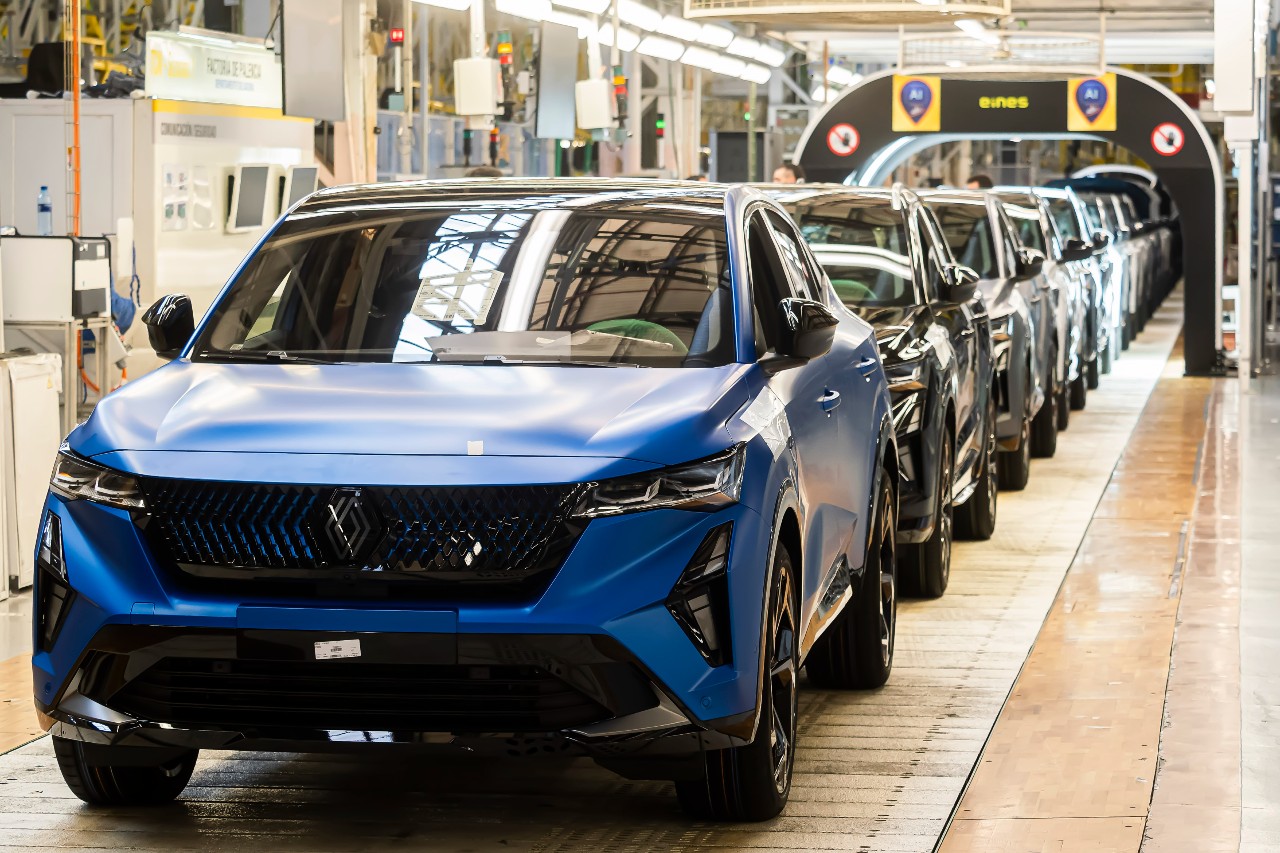
Alors que l’industrie automobile évolue à une vitesse sans précédent, le groupe Renault réinvente depuis quelques années son approche de la production. Cette révolution du système industriel du constructeur français a démarré en décembre 2023, dans les 25 usines du groupe réparties dans pas moins de 13 pays, avec le lancement du plan Re-Industry 2027. Son objectif ? Permettre au groupe Renault d’être plus rapide, plus compétitif mais aussi résolument plus agile. Le tout, en un temps record.
Concrètement, le constructeur au losange souhaite réduire de 50 % les coûts de production pour un véhicule électrique et de 30 % pour un thermique. Le temps de développement d’une voiture doit quant à lui être divisé par deux, passant de quatre à deux ans, tandis que le délai de fabrication doit être réduit à dix heures par véhicule. Enfin, le groupe Renault envisage de baisser de 40 % la consommation énergétique de ses usines d’ici à 2027.
À mi-parcours, le plan a ainsi atteint plus de la moitié de ses objectifs. À titre d’exemple, le groupe produit actuellement sa dernière R5 en seulement dix heures dans son usine de Douai (59), et celle-ci comporte 25 % de pièces en moins que la Megane E-Tech, lancée en 2022.
Autre exemple, le temps de développement visé pour la future Renault Twingo est de deux ans, contre quatre ans pour la Megane E-Tech. Enfin, pour ce qui est de sa performance énergétique, Renault l’a déjà améliorée de 26 % entre 2021 et 2024, lui permettant d’être sur la bonne voie pour atteindre l’objectif qu’il s’est fixé.
"Notre plan Re-Industry 2027, lancé fin 2023, a embarqué l’ensemble de notre base industrielle dans un vaste processus de numérisation. Et les résultats dans nos usines sont déjà tangibles. Nous avons placé la digitalisation et l’intelligence artificielle au cœur de notre fonctionnement, et nous en voyons déjà les résultats sur le terrain. Le groupe Renault dispose aujourd’hui d’une base industrielle moderne, rapide, agile et interconnectée, dans des usines construites il y a plusieurs décennies. Ce haut niveau de flexibilité renforce notre compétitivité", souligne Thierry Charvet, directeur de l’industrie et de la qualité du groupe Renault.
L'usine de Palencia, fleuron technologique du groupe Renault
Pour atteindre les objectifs du plan Re-Industry 2027, l’intelligence artificielle et la digitalisation ont donc été fortement déployées dans les usines du groupe Renault. En première ligne, on retrouve le site de Palencia, en Espagne, où sont produits 139 000 exemplaires du Rafale, de l’Espace et de l’Austral.
Inaugurée en 1978, l’usine a été profondément modernisée pour pouvoir accueillir les différentes technologies nécessaires à cette mutation. Aujourd’hui, ce sont ainsi pas moins de 800 outils faisant appel à l’IA qui ont été déployés dans l’usine de Palencia.
Parmi les innovations majeures, l’usine Renault de Palencia a été la première à mettre en place l’outil "Plant Connect" au sein du groupe, alors qu’il est encore en phase de déploiement dans les autres usines à travers le monde. Ce système permet de suivre en un seul endroit et en temps réel tous les indicateurs du processus de production des véhicules, grâce à 380 installations connectées dans le site et plus de trois millions de datas qui sont envoyées dans le "cloud" chaque minute.
Les différents indicateurs (qualité, coûts, délais, consommation d’énergie…) sont alors centralisés sur l’écran principal, offrant de fait une vision à 360 degrés, allant de la commande à la livraison du véhicule au concessionnaire. Enfin, l’outil peut aussi émettre des suggestions d’actions prédictives, qui s’appuient sur des règles logiques et des algorithmes soumis par l’IA. Au final, cet outil centralisé permet d’améliorer la surveillance des opérations, mais surtout de réduire le temps de réponse des équipes de Palencia.
Un métavers industriel
Pour améliorer son efficience industrielle, le groupe Renault a également déployé, depuis 2019, un métavers. Cette plateforme conçue et développée par les équipes du groupe a radicalement transformé, et entièrement digitalisé, le fonctionnement industriel et la chaîne d’approvisionnement du constructeur.
Et pour cause, le métavers permet d’obtenir un jumeau numérique de chaque usine, véhicule, équipement ou outil de production. Le groupe en utilise aujourd’hui plus d’un million, dans le but d’exécuter des simulations avancées sans avoir à réaliser l’opération physiquement, ce qui améliore drastiquement la performance de ses usines. Pour que cela fonctionne, tous les sites doivent désormais être connectés sur un réseau wifi et interagir via un cloud.
Au total, sur l’ensemble des sites de production du groupe Renault, on totalise plus de 20 000 équipements majeurs qui rapportent plus de cinq milliards de points de données par jour. Ces données sont par la suite utilisées par les équipes opérationnelles, afin de réaliser de la maintenance prédictive ou du contrôle qualité par photos. Sur chaque véhicule, ce sont donc pas moins de 3 000 contrôles qui sont réalisés par l’IA sur les lignes de production des différentes usines.
Ainsi, Renault estime que, grâce à son métavers, la fiabilité de ses véhicules a plus que doublé en l’espace de cinq ans. "Grâce à notre métavers industriel, qui est désormais opérationnel sur tous nos sites, nous pouvons superviser toutes les opérations, y compris les plus basiques, en temps réel, partout dans le monde. Ce jumeau numérique nous permet de réagir immédiatement en cas d’anomalie, d’optimiser la maintenance, d’améliorer la qualité et d’accélérer les décisions", assure Thierry Charvet.
Un condensé d’innovations technologiques
Mais concrètement, quels outils sont utilisés via l’intelligence artificielle ? D’abord, l’usine de Palencia du groupe Renault a développé un scanner 3D portable qui examine la géométrie de la pièce et la compare aux modèles existants, afin d’identifier les éventuelles imperfections et in fine de garantir sa conformité. Facilement transportable, ce "gant" en fibre de carbone permet donc de réaliser 4,9 millions de mesures par seconde, avec une précision micrométrique, pour un temps d’inspection complet de cinq minutes maximum.
Conçu par Renault, ce scanner 3D permet de détecter les imperfections de carrosserie sur les véhicules. ©Renault
La technologie Double AI permet quant à elle d’aider les opérateurs à optimiser la gestion de leurs tâches. Déjà intégrée aux systèmes Adas de nos véhicules pour la lecture des panneaux de signalisation, cette technologie de vision par IA détecte les anomalies dans les processus de production, comme l’absence d’une pièce ou des problèmes au niveau des soudures par exemple. À Palencia, Renault dispose déjà de 25 postes de contrôle et de près de 1 000 points de vérification par l’IA.
Les équipes de Renault ont aussi développé un système permettant de valider la connectivité de manière automatique et précise. En d’autres termes, cette technologie peut par exemple s'assurer que l’essuie-glace ou les feux arrière sont correctement connectés. Un moyen de confirmer que les modules et les connexions électriques sont pleinement fonctionnels avant d’entrer dans la chaîne de production, et donc d’éviter des ajustements coûteux de dernière minute.
À la sortie de la chaîne de production, tous les véhicules de l’usine de Palencia passent par un tunnel qui les soumet à une dernière inspection. Et pour cause, cette arche utilise plus de 50 caméras haute définition prenant plus de 112 photos par véhicule, afin d’inspecter avec haute précision la conformité de chaque voiture et d’optimiser leur qualité. Si le système détecte un problème nécessitant une correction, il indique alors à l’opérateur la marche à suivre.
Enfin, le site de Palencia a également mis en place des technologies de pointe visant à répondre aux plus hauts standards de qualité, de sécurité et de confort. L'une d’entre elles détecte précisément les sources de bruit via 120 microphones, dans le but d’améliorer de manière significative le confort acoustique à bord des véhicules.
Ici, la capacité de détection de bruit est ainsi cinq fois supérieure à celle de l’oreille humaine. On peut aussi relever le système de surveillance de la température des dégivreurs de lunette avant et arrière, qui évalue l'efficacité de tous les éléments chauffants intégrés.
Sur le même sujet
Laisser un commentaire
Vous devez vous connecter pour publier un commentaire.