Performance et compactage : le nouveau défi des usines du groupe Stellantis
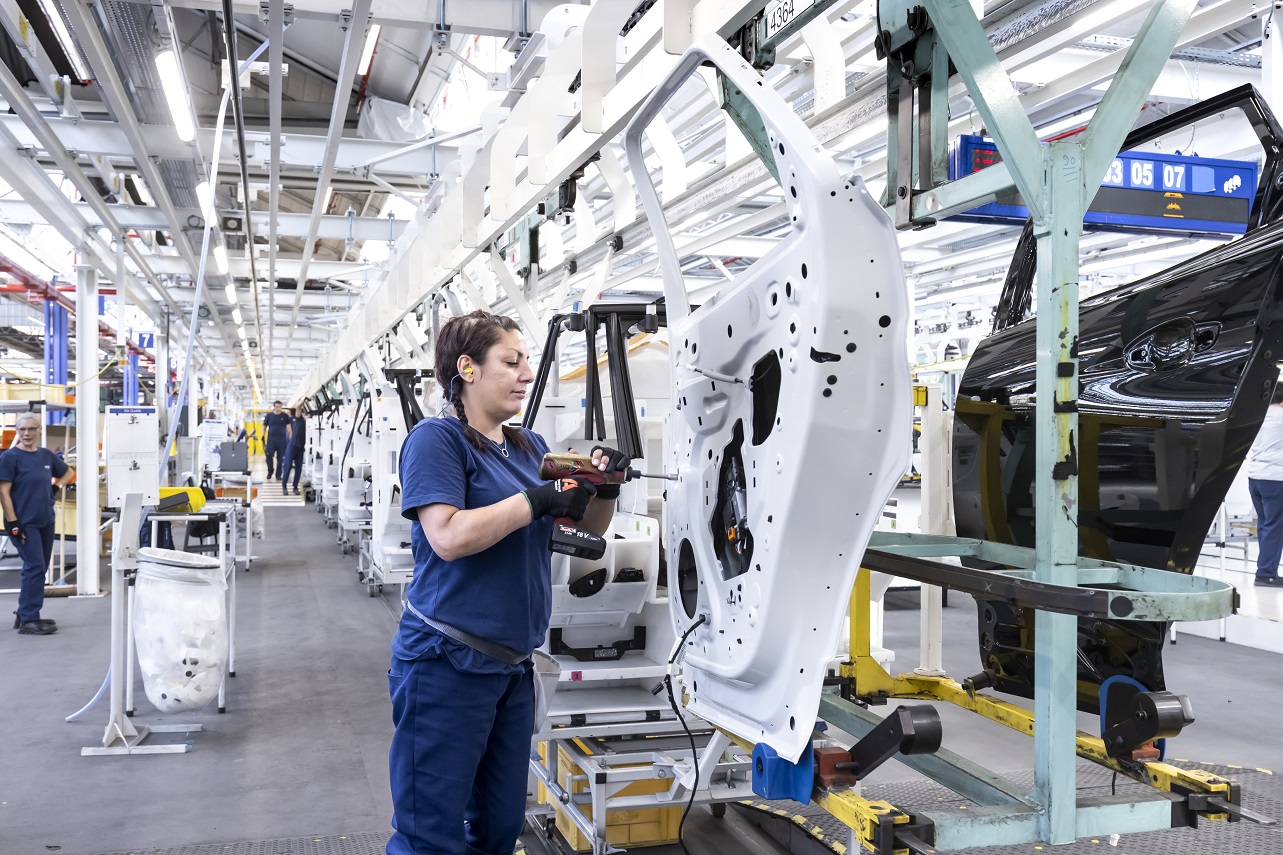
C'est désormais un rituel pour les directeurs d'usine du groupe Stellantis : chaque mois, ils attendent avec impatience que tombe le classement des 92 sites de production dans le monde. Au menu, niveau de la qualité (calculée en pourcentage par millier sur les retours clients), les coûts et le coût total de la production.
Selon Arnaud Deboeuf, chief manufacturing du groupe Stellantis, la pratique permet d'échanger sur toutes les méthodes et services efficaces qui peuvent être déployées. "C'est la force de frappe de notre manufacturing, d'avoir pu créer une vraie communauté, une équipe multiculturelle permettant les échanges de technologies. Dans cette période où l'automobile vit la plus grande crise qu'elle ait jamais vécue, c'est une vraie force", explique-t-il.
Le Covid, la pénurie de semi-conducteurs, l'inflation, les prix de l'énergie… le contexte est particulièrement difficile pour l'automobile et la production doit devenir un avantage compétitif. Si celle-ci ne pèse que 10 % du coût total d'un véhicule, les patrons d'usine sont responsables de la totalité de ce coût. Une implication qui leur laisse la possibilité d'agir sur de nombreux leviers, comme les achats, le design intérieur ou encore l'ingénierie. Il faut trouver une nouvelle productivité pour absorber les coûts de l'électrification des véhicules. "Le fait de donner la responsabilité des coûts de production aux directeurs de sites est essentiel car la survie des usines est en jeu", avance Arnaud Deboeuf.
Compactage et modernisation
Aujourd'hui l'heure est au compactage. "Nous ne sommes pas des propriétaires fonciers", s'amuse Arnaud Deboeuf. Il faut donc réduire les superficies, repenser les flux logistiques de pièces, produire au plus juste et baisser les surfaces occupées. Vendre les terrains pour permettre de nouveaux investissements est également l'un des enjeux. Car qui dit plus petite surface, dit également, économie de chauffage, d'électricité, gain de temps grâce à l'optimisation des process. C'est notamment le cas, à Sochaux, berceau historique de Peugeot, qui s'est séparé de 44 hectares de terrain, revendus au pays de Montbéliard, et qui va accueillir un nouvel investisseur, BT Immo Group, un gestionnaire d'actifs immobilier.
A lire aussi : A Sochaux, Peugeot se réorganise pour améliorer sa performance
L'usine 4.0 n'est pas un vain mot. Le suivi de production est digital, tout comme la connexion entre les différentes unités du site d'assemblage. L'investissement de 8 millions d'euros réalisé dans la mise ne place d'un transtockeur pour la logistique des pièces le prouve. La ligne d'assemblage appelle automatiquement les pièces dont elle a besoin pour poursuivre la production.
L'organisation humaine bénéficie également d'une nouvelle stratégie. Tous les sujets qui peuvent poser problèmes sont mis en commun avec tous les directeurs d'usine avec une finalité : créer une communauté, baptisée Teamtowin.
"Notre grande fierté se traduit par nos résultats puisque notre indicateur qualité, qui se base sur les retours des clients, montre une amélioration de 25 % des avis négatifs par millier de voitures, soit proche du niveau de Toyota, qui reste notre benchmark en la matière", reconnaît Arnaud Deboeuf.
Réinternalisation de certains process
Des réorganisations qui deviennent cruciales en ces temps de flambée des prix de l'énergie. Parc photovoltaïque, diminution du chauffage, de la climatisation, baisse de l’éclairage, toutes les pistes sont étudiées pour faire baisser une facture qui s'annonce sévère.
Autre piste pour améliorer la productivité : la réinternalisation de certains process comme l'injection plastique pour les pare-chocs, la fabrication des cockpits sur les 3008, ou même les assemblages des intérieurs de portes. Mais le mouvement est large puisque l'assemblage d'une partie des batteries sera géré par ACC, dans le Nord de la France, celui des moteurs a été confié au site de Trémery.
"Pendant un certain temps, l'industrie automobile a voulu baisser les investissements mais il n'y a pas de raison que nous soyons moins performants que les équipementiers", note Arnaud Deboeuf. De fait, chaque tâche fait l'objet d'une analyse sur ce qui est possible (et rentable) d'internaliser ou non.
Le process est donc en marche et toute la valeur qui peut rapatriée le sera. Chaque usine fait l'objet d'un plan "want to be" à deux années. A charge des directeurs de site de présenter leur projet de développement et de performance. Tous les ans, 20 projets sont sélectionnés et présenté à Carlos Tavares, le directeur général du groupe.
Sur le même sujet
Laisser un commentaire
Vous devez vous connecter pour publier un commentaire.