Développer la force pédagogique du crash-test
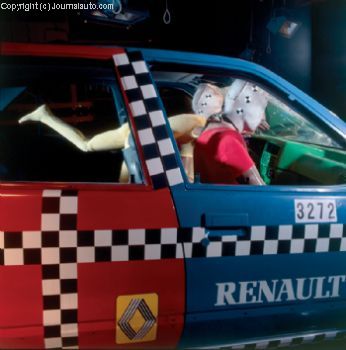
...guise de clou du spectacle. Commentaires.
Le prélude tient en une date, subjective mais symbolique : 1968. La ceinture de sécurité devient alors obligatoire à l'avant, en France comme dans de nombreux pays européens. A l'heure où la sécurité est devenue un enjeu névralgique dans le monde automobile, ce repère temporel permet de mettre en évidence que la protection des passagers du véhicule reste une problématique relativement récente. Mais aujourd'hui exacerbée. Sur une vaste toile de fond de civisme et de respect de la vie dressée par les pouvoirs publics, les constructeurs se sont lancés dans une course à l'innovation pour la sécurité. Course d'autant plus échevelée que la sécurité s'est peu à peu muée en argument commercial de premier ordre. La foison des publicités des constructeurs sur ce thème en témoigne, ainsi que la transformation des résultats Euro NCAP en messages marketing. Parmi les constructeurs les plus investis dans ce travail, on trouve notamment Renault. Le constructeur français géométrise ses recherches sur la sécurité en triptyque : le Technocentre héberge l'unité des crash-tests virtuels réalisés via CAO ; le site d'Aubevoye se focalise sur la problématique des liaisons au sol ; enfin, le site de Lardy accueille les équipes spécialistes des crash-tests réels. Au total, 600 personnes se dédient à l'amélioration de la sécurité des véhicules au sein du groupe, avec des champs de compétences variés (médecins spécialistes en biomécanique, ingénieurs, techniciens experts en matériaux, en électronique, techniciens d'essais…). A titre indicatif, on peut rappeler que le budget annuel pour la sécurité est de l'ordre de 100 millions d'euros, ce qui représente plus de 5 % du budget R&D de l'entreprise.
A Lardy, Renault effectue près de 400 crash-tests réels chaque année
Au sein du dispositif Renault, le centre technique de Lardy, qui fut créé en 1951, notamment pour les premiers essais de résistance aux chocs, alors très sommaires, reste essentiel. En effet, si les crash-tests virtuels présentent le précieux avantage d'offrir des opportunités de simulation avant la production du modèle et qu'ils sont significativement moins coûteux, les crash-tests réels demeurent incontournables. Pour la richesse et la précision des mesures, la voie empirique reste donc largement exploitée et Renault sacrifie ainsi chaque année entre 350 et 400 véhicules de série sur l'autel de la sécurité. Nous avons eu l'opportunité d'assister au crash-test d'une Modus dans une configuration assez violente : un choc frontal asymétrique contre un mur à une allure de 65 km/h. Le véhicule affiche une masse de 1 440 kilos et embarque quatre personnes : le conducteur, le passager avant et, à l'arrière, un enfant sur rehausseur et un enfant installé dans un siège enfant. On peut rappeler que la Modus est la première voiture de sa catégorie à avoir obtenu cinq étoiles au test Euro NCAP, avec une note flatteuse de 32,84 points sur 37. Les derniers préparatifs avant le crash-test sont d'une grande minutie et l'ambiance est scientifique. Pour parvenir à une vitesse de choc élevée, les techniciens de Renault utilisent une catapulte qui correspond grosso modo, en termes de puissance, à un moteur de 1 200 ch. Quand le signal retentit, la Modus est donc projetée à 65 km/h contre un "mur". Le fracas fait sursauter l'assemblée, pourtant prévenue… Bien que l'allure de 65 km/h puisse sembler modérée, le véhicule s'apparente bel et bien à une compression de César après le choc, sauf que l'habitacle est préservé. Les quatre mannequins, entourés par les airbags flottants et l'odeur de brûlé des ceintures, n'ont guère bougé. A l'exception du plus petit enfant qui a les bras relevés, ce qui révèle les principaux contours de la question de la sécurité pour cette classe d'âge : la prise en compte d'un rapport de poids entre tête et corps spécifique, et les enjeux clefs de la souplesse des petits et de la fragilité de leur nuque. Les techniciens de Renault peuvent alors s'affairer autour du véhicule, réaliser les premières constatations de visu et procéder au relevé méthodique des informations liées à la voiture et à ses occupants. Sur la base d'un choc d'une fraction de seconde, les équipes de Renault collectent une pléiade de données qui nécessitent plusieurs centaines d'heures d'analyse. D'autant que chaque crash-test est aussi filmé par une quinzaine de caméras high-tech.
La vocation didactique du crash-test devrait être mieux exploitée auprès du grand public…
Ces caméras filment à la cadence effrénée de 1 000 images seconde (contre 24 images/seconde pour un film ordinaire), permettant ainsi d'analyser dans le détail des chocs dont la durée est de l'ordre de 100 à 150 millisecondes ! Il s'agit d'un matériel très coûteux utilisé aussi dans le secteur aéronautique et par les militaires. La vidéo rapide permet aussi d'étudier le phénomène d'ouverture de l'airbag. En effet, un airbag se gonfle en 30 millisecondes environ, "un battement de cils", dixit Aimé Le Calve, responsable de la section essais sécurité passive au centre technique Renault de Lardy, et se dégonfle aussitôt. En outre, au moment du gonflage, la vitesse d'expansion peut dépasser les 300 km/h. Au-delà des recherches de conception réalisées en amont par les fournisseurs, l'amélioration de ce dispositif de protection active passe aussi par la vidéo rapide. A l'issue du crash-test de la Modus et avant les longues heures d'analyse à suivre, deux remarques, d'une nature tout à fait différente, pouvaient être faites. Primo, au cours des dix dernières années, des progrès considérables ont été accomplis dans le domaine de la résistance aux chocs. Ainsi, Aimé Le Calve souligne qu'avec "un crash-test identique réalisé sur une Super 5, véhicule qui roule encore aujourd'hui, la porte serait réduite à une longueur de 30 centimètres". Secundo, le crash-test est une démonstration qui mériterait d'être davantage exploitée auprès du grand public dans une optique de prévention routière. Sa dense dimension didactique a la force de l'évidence. Les techniciens de Renault le reconnaissent volontiers, mais ils objectent parallèlement qu'il est périlleux pour un constructeur d'associer son nom et ses modèles à l'événement traumatique que représente l'accident. Il y a quelques années, Citroën avait bien franchi le pas, mais par le truchement d'un top model de renom… La donne était donc un tantinet faussée. En fait, il faudrait qu'un organisme fédérateur ose utiliser le potentiel éducatif du crash-test. En effet, contrairement aux mises en scène de faits divers jouant uniquement sur le pathos, le crash-test ne se limite pas au simple registre affectif.
La durée de la loi de décélération est de 80 millisecondes !
Si l'espace "crash-test" occupe une large place au sein du centre de Lardy, ce dernier dispose aussi de nombreux autres ateliers dédiés à la sécurité. Visite non exhaustive avec Aimé Le Calve, qui assène en guise de préambule : "Tous nos tests sont réalisés en estimant que le conducteur et les passagers ont accroché leur ceinture. C'est vraiment le B.A.BA de la sécurité. Sinon, ça ne sert à rien de trouver de nouvelles solutions." La ceinture, cet élément basique qui a considérablement évolué au fil des ans. Avec la première Mégane, Renault a ainsi innové avec la ceinture à limiteur d'efforts. Conjugué à l'airbag, cette ceinture permet de réduire les efforts appliqués sur le thorax (la pression se trouve alors limitée à 400 daN) en cas de choc. "A partir d'un certain stade, il est inutile de chercher à retenir le passager car le risque de l'écrasement du thorax est sérieux. Mieux vaut donc le "relâcher" en maîtrisant cette opération, bien entendu", explique Aimé Le Calve. La première salle de test, architecturée comme un laboratoire, accueille des espaces de mesures et de préparation au crash-test. Ainsi, un technicien travaille sur une Logan en effectuant un relevé de points dans l'espace sur les portes par rapport à un repère central. Ces points seront utilisés après le crash-test pour fiabiliser et affiner les mesures. La précision est donc de mise même si elle ne confine pas à l'obsession. "Nous ne sommes pas attentifs au millimètre près mais, en revanche, rien n'est aléatoire", glisse le technicien. Un peu plus loin, on trouve l'atelier réservé à la catapulte à Sandow. Le principe est simple : un chariot, accueillant un - ou plusieurs - mannequin, vient percuter des tubes fixés au sol, reproduisant ainsi le phénomène de décélération. Pro memoria, rappelons que la durée de la loi de décélération est de 80 millisecondes. Ce système permet de mesurer la retenue des éléments structurels et de tester des enrouleurs. Ce jour-là, l'enrouleur testé ne donnait pas satisfaction aux techniciens de Renault. Le fournisseur perdait donc ses chances d'être homologué. "Ces essais sont peu coûteux et nous pouvons en faire beaucoup", déclare Aimé Le Calve, avant d'ajouter : "Même si les négociations sont parfois âpres avec le département achats, nous avons un réel droit de veto si nous estimons que le matériel n'est pas à la hauteur des exigences de sécurité du groupe." Une autre salle est dédiée aux tests de résistance des sièges. On y trouve un "instrument de torture" qui met à l'épreuve les sièges des différents modèles de la marque. Cette activité est devenue très importante avec la progression de la modularité des véhicules et le développement des sièges escamotables. En face, Stéphane Faucher, technicien responsable du choc piéton, nous convie dans son atelier. "Notre principal objectif est de parvenir à un maximum d'absorption du choc par le véhicule", résume-t-il, avant d'énumérer quelques techniques efficaces : "Nous utilisons des pains de mousse, des systèmes d'absorption, des systèmes fusibles et des systèmes rétractables. Nous travaillons aussi actuellement sur des capots déplaçables." Dans ce domaine, les tests se déclinent en deux familles : les tests "jambes", centrés sur le triptyque fémur-tibia-genou, et les tests "tête", respectant un distinguo enfants-adultes.
Les mannequins sont des mini-laboratoires bardés de capteurs qui coûtent 150 000 euros l'unité
A proximité de l'atelier "chocs piéton", un test sur un prétentionneur d'airbag est réalisé dans le secret pour la remplaçante de la Laguna. Enfin, en changeant de bâtiment, on arrive dans la fameuse salle des mannequins. Au fil du temps, les mannequins sont devenus des mini-laboratoires bardés de capteurs (capteurs accéléraux, capteurs de déformation, capteurs efforts-moments et capteurs de mesures de vitesses angulaires). Sur certains mannequins, on peut trouver jusqu'à 60 capteurs. Il existe plusieurs types de mannequins (pour choc frontal, choc latéral et choc arrière), plusieurs familles de mannequins (homme, femme, enfant de moins de 2 ans, de 4 ans et de 10 ans) et plusieurs tailles de mannequins (S, L, XL). "Nous pouvons ainsi adapter nos tests et affiner nos analyses en fonction de la biomécanique de chacun", synthétise Aimé Le Calve. En revanche, il n'existe pas de mannequin de femme enceinte, par exemple. Dans ce cas, Renault a recours aux tests virtuels. Notamment pour des raisons de coûts car il faut savoir qu'un mannequin de dernière génération (de type Hybrid III, Thor, Wordsid…) coûte en moyenne 150 000 euros. Bref, en sortant de Lardy, on mesure à quel point les constructeurs, en l'occurrence Renault, progressent dans le domaine de la sécurité. On se dit aussi que "la peur du gendarme" qu'on nous vend sans trêve comme la méthode miracle pour améliorer la sécurité routière a des côtés bien politiciens, voire électoralistes… On en revient presque à la dimension didactique du crash-test.
Alexandre Guillet
* Association des journalistes techniques européens
Voir aussi :
Sur le même sujet
Laisser un commentaire
Vous devez vous connecter pour publier un commentaire.